
So a drilling fluid with a well-designed fluid rheology should be pumped in the well with high velocity to improve cutting transport and avoid accumulation of cutting in the horizontal and deviated section of the well. Studies found out that turbulent flow regime performed better at high angles. So, lots of studies were carried out to develop a good procedure in cutting transport. Even, this will be most critical particularly in case of extended reach drilling where larger and longer wellbores are drilled. Optimization of this power will be very critical in the directional and horizontal well when cleaning is common and costly problem. This hydraulic power will then be helpful in hole cleaning and removal of cuttings out of the well. Theoretically, most of the hydraulic power should be utilized by the bit. Determination of pressure drop at the bit is one of the major concerns for establishing proper hydraulic design. In addition, accurate quantification of system losses (we already discussed in the previous sections) enhances the validity of calculated equivalent circulating density (ECD) and other drilling parameters and indicators.
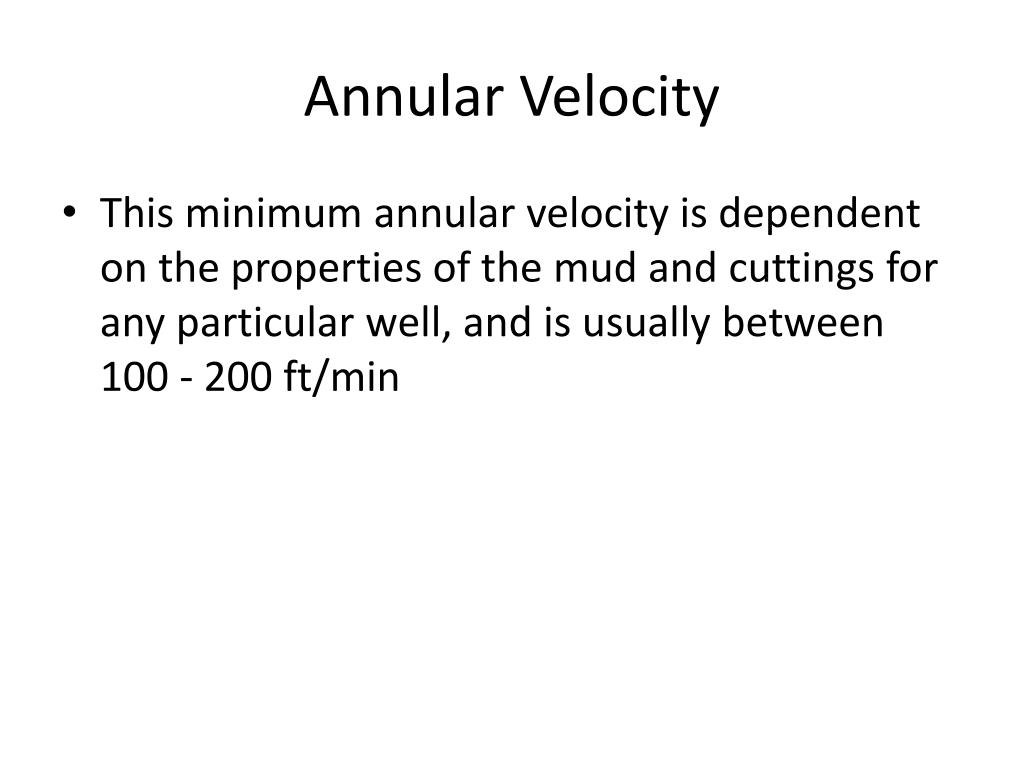
Table 2.21 shows a summary of the variables and constrain parameters that are involved in a typical drilling operation. One can obtain maximum/minimum for one or more dependent variables within boundaries imposed by the cost, safety, and physical properties of the analyzed system. (1994) stated that drilling hydraulics optimization involves manipulation of several independent variables. However, unnecessary predefinition of key independent variables can lead to less-than-optimal results. Reduction in the number of parameters can simplify computer algorithms and increase chances of converging on a solution, particularly when multiple, narrow boundary conditions are involved. (1994) are among the first ones who advocated this approach, especially when considering a large number of parameters. Critical characteristics of many of today’s wells, on the other hand, have made it advantageous and even necessary to rely on computer technology to execute the bit hydraulics optimization process. It also covers the improvement in the underbalance drilling (UBD) optimization using aerated fluids. This section discusses the current development in hydraulic optimization using down-hole motors and its improvement in overall drilling optimization. For example, Fulletron charts, Amoco curves, the use of optimization theory to maximize some arbitrary functions such as maximum bit hydraulic horsepower or jet impact force are among them.

There are lots of empirical correlations to optimize hydraulics. Drilling hydraulics is mainly discussing the pressure needed during drilling to improve drilling and provide sufficient cutting removal capacity and decreasing pressure losses in the circulating system. Drilling hydraulic optimization with conventional drilling fluid is a well-known practice which has been widely practiced in the oil industry.
